A High Speed Troubleshooting System for the Print Industry
At the heart of the Procemex system is a Procemex Flex camera. It is a dedicated intelligent camera with on-board RAM memory and DSP processors and it is developed by Procemex engineers over the past 5 years.
It combines for the first time excellent light sensitivity, fast frame rates and high resolution. It can cover with its versatility a printing press from splicer to folder area. The cameras are connected with standard TCP/IP network with system server, where data is stored for later analysis.
Procemex Piccolo Flex –professional troubleshooting
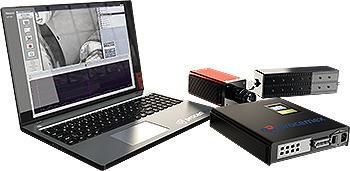
As the camera has intelligence built-in, it can provide with a standard laptop computer a high speed troubleshooting system without comparison. This capability to connect intelligent cameras with standard laptops also forms the platform for Procemex Piccolo Flex system. This is a system of choice for all professionals who need to perform troubleshooting with carry-on size equipment.
Turn your own laptop into a high speed camera system

As the Procemex Flex camera processes and prepares all video and data files, you can connect it with a standard network cable to your laptop and have a state of the art high speed camera system to troubleshoot any part of your operation.
Metal halide or strobe LED lights

Both continuously burning metal halide lights and strobe LED lights are available with the system. Metal halide lights offer a cost effi cient solution for illuminating paper web and machine sections. Strobe LED lights, developed by Procemex offer a solution where lights are seamlessly integrated with cameras.
The Procemex Flex camera fully automatically controls the strobe lighting to match the camera frame rate, with camera shutter speeds automatically controlling each light pulse length. This means the strobe light is illuminated only when the camera is filming. This powerful strobe lighting uses on average 30W to eliminate heat and energy consumption problems.
Data acquisition and communication
As it is necessary to transfer press and paper roll related information in both directions Procemex offers interfaces with several third party suppliers such as Pecom interface with manroland.
Procemex PRINT also features a bar code reader solution for customers not able to automatically provide roll numbers.
Web breaks can occur during the washing sequence, but there can be several reasons for this.
For example, was the web break caused from excess water in the cylinder gaps, or ink/water drops, or because of paper damage?
A reliable analysis on the origin of this type of problem comes from optimised monitoring by multiple cameras located in the right positions. Procemex, the leader in paper and web printing monitoring, recommends a minimum 3-4 cameras configuration for a web offset press. This will have:
- 1-2 cameras at the paster to monitor the web being unwound from the roll.
- 1 colour camera before the dryer to monitor the printed web, and also the end of the washing cycle and the restart of printing.
- 1 camera in the folder superstructure after the slitters will indicate the position of the web break in the press line – did it break in the dryer or in the folder area?
While each camera has its own specific tasks, it is only when they all work together that they give the most information to determine what really happened in the machine that caused a web break. To make the cameras work together they are synchronised to the same piece of the paper web to allow them to track back to any web breaks from the superstructure to the printing units or the paster.
The examples show a web break caused by the paper and a web break caused by the black printing unit. On both web breaks the first indication was when a break happened in the folder area (tension loss on one ribbon). Viewing the pictures from the superstructure camera back to the unwind showed the real reason for the web break.

- Ribbon break.
- Detectable edge damage on B-side.
- Edge damage before the dryer.
- Edge crack at the paster unwind.
- Cut in machine direction.
- Holes caused by the catching unit (blue).
- No indication at the paster so damage caused by printing unit, the break occurred in the black printing unit. In the text are trademarks of their respective owners.
Troubleshooting in folder area

Printers have requested to be able to analyse problems inside of tightly built folder areas. Procemex has extended the system to offer two applications to view critical folder positions.
- On-line grabber monitoring to adjust grabbers on gravure presses
- Folder troubleshooting tool for web offset presses.
As the viewing area is quite limited and a higher frame rate is necessary, a special digital Procemex Flex Folder camera is applied here. The folder camera continuously films paper web with press mechanics and stores several minutes of video in intermediate RAM-memory inside the camera. In connection with a web break, folder jam etc, the data is transferred automatically to the system and can be analysed afterwards in slow motion exactly as with other cameras.
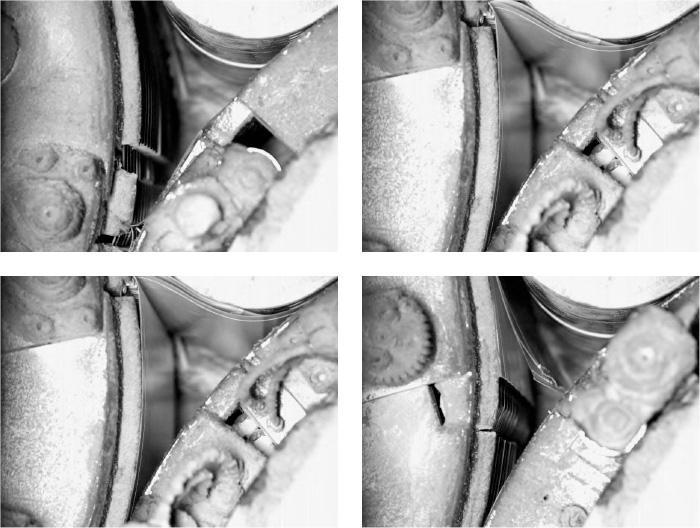
WebAccess 2.0
The idea behind the Procemex WebAccess communication platform is to enhance and accelerate communication between printers and their suppliers to allow them to share critical information rapidly, reliably and safely among all related parties.
Traditionally, disturbances on press that cause machine downtime or quality issues are analysed and solved internally, in some cases third party technical specialists may need to be consulted or visit the site to help resolve an issue. This analytical process can now be undertaken more rapidly and efficiently by integrating remote access monitoring technology into the communication chain. Procemex WebAccess allows printers to show specific press disturbances to invited third party partners such as machine builders, technical consultants and paper suppliers.
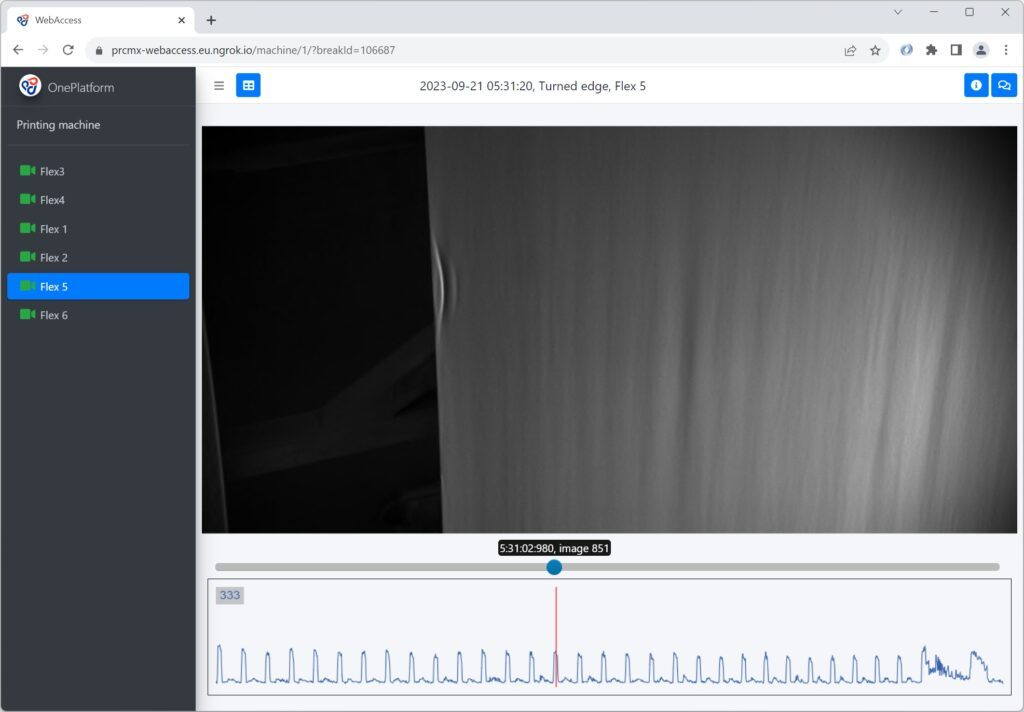
Third party suppliers can access and analyse online press disturbances from the printing:
- Events automatically include all relevant data from machine number, break time, machine speed, roll number, paper grade, paper supplier, image change graph etc.
- Light IT infrastructure that is simple and safe to access from a PC with an Internet connection.
The printer selects events to a library that gives remote users the same view as the printers at the press. The view includes all relevant data for a complete chain of evidence: machine and paper related data, time stamps, analysis graphs, as well as manual data of pre-analysed results.
Preview pictures with markings allow direct access to the root cause chosen by the printer. The system provides paper suppliers with online information to assess paper related issues and potential claims. Third party suppliers can only access the events related to their own equipment, paper or other consumable.
A View from a paper supplier
We permanently use Procemex WebAccess to enter published events that all our production plants have access to. It has become a very helpful tool to get a much greater understanding on what happens to our product when it’s going through the press.
It has opened new doors to improve our paper performance; for example the profile variations seen in pictures 1 and 2 gave us the right hints for improvements to be made during the paper making stage
UPM
A View from a Gravure Printer
We have been working for more than two years with Procemex WebAccess and in my opinion it would be impossible to handle all the web breaks from our 11 printing machines without it. We even have a WebAccess account for ourselves and use its mailing function to be informed of any web break occurring on any of our presses selected per supplier.
At the start of each day I check my email account to set my daily priorities. After an investigation of the issues I publish events like paper related breaks, and then discuss those with the highest priority with the technical service of each paper supplier. These methods enables me to handle all the web breaks from our 11 machines in a benchmark best practise manner.
Mr. Hösl, Prinovis Ltd. Nürnberg
A View from an Offset Printer
WebAccess has reduced our workload on preparing claims because we no longer need to export images and data onto a DVD, or convert them to different formats. We believe paper suppliers feel the same way.
Ms Carl and Mr Ronig, Weiss-Druck GmbH & Co.KG.
Why on-line communication with Procemex Web Access?
Today´s marketplace sets completely new requirements for the quality, type and speed of communication between printers and papermakers.
- Trustworthy security tagged evidence material brings both parties reliably onto the same page
- Faster feedback helps to to reduce off-spec paper production
- Long physical distances between printers and paper suppliers (time, travel cost)
- Camera systems shed light onto unknown issues
- One person in printing company handles more presses than before
- One technical customer service person handles more print customers than before